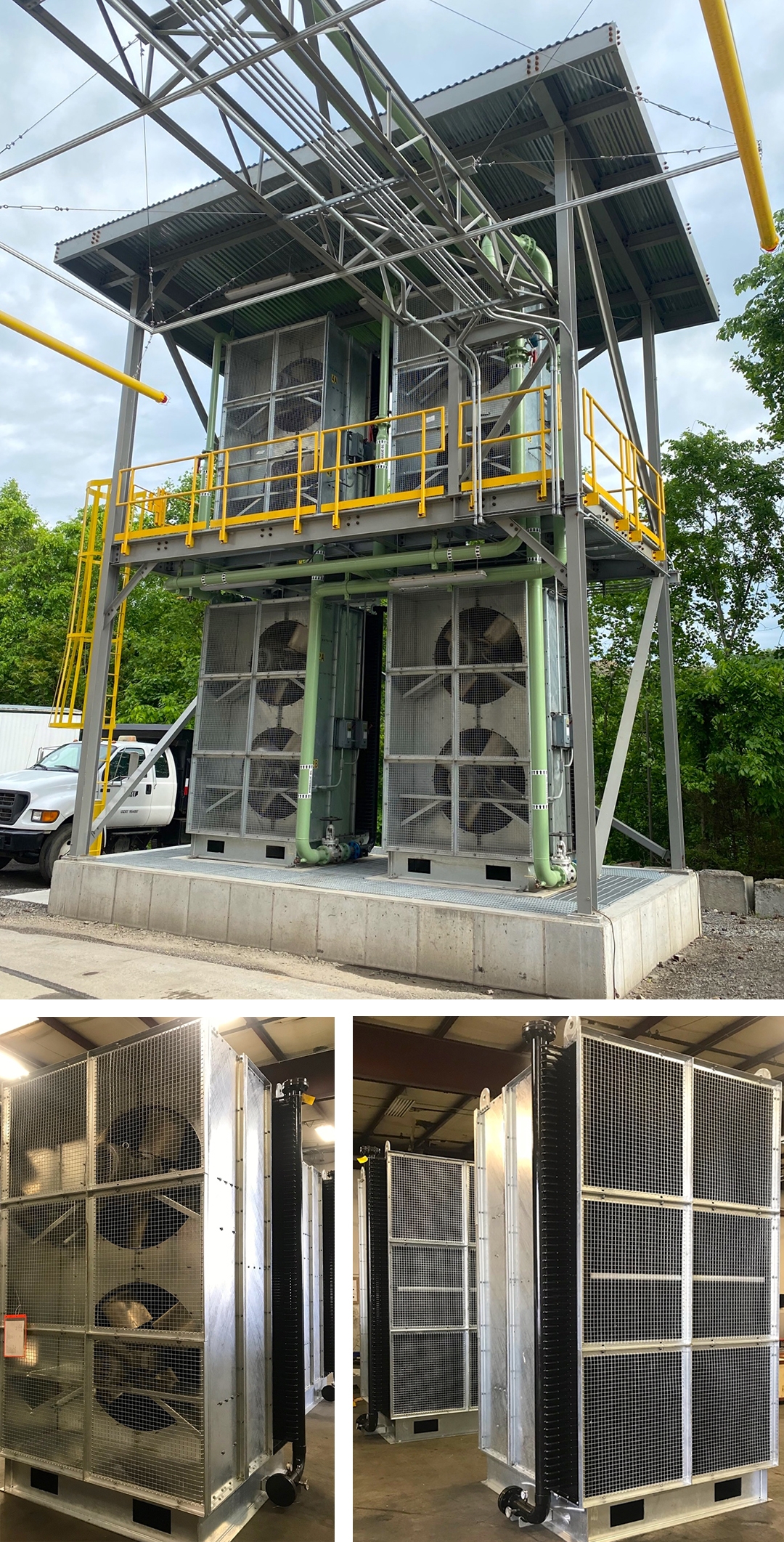
Large Industrial Forge Plant
Hayden solution saves industrial forge plant tens of thousands a month in wastewater costs
Challenges
Our customer originally had dry coolers that were not meeting demand for their oil cooling loop. To compensate for the capacity shortage, they installed a secondary cooling loop that utilized a shell and tube heat exchanger which used city water to provide cooling for the oil process. Due to the secondary loop being installed for emergency purposes, the water passed through the shell and tube heat exchanger once and was then disposed of. This process was costing the customer tens of thousands of dollars in water consumption and waste. The customer knew they needed to eliminate the secondary water cooling loop; however, they were not confident that simply installing dry coolers was going to correct the problem.
Solution
Hayden worked with site engineers to ensure a proper design and installation. The new installation featured the following changes:
- Technical Evaluation
- Changed the ambient design temperature based on the site conditions for proper cooler sizing.
- Increased the required design heat load based on the evaluation of the temperature and flow rates recorded from the process.
- Installation Changes and Cooler Features
- Relocated the dry coolers away from the exhaust air coming from the building to lower the intake air temperature into the coolers.
- Temperature and pressure gauges were supplied on all connections so the client could quickly identify if the coolers were experiencing flow or temperature issues.
- Bundles included an external protective coating that offers a five-year corrosion guarantee. The coating will extend the life and performance of the coolers over time.
TESTIMONIAL
Here's what the customer had to say after the coolers were in operation for one year: “The coolers performed very well during this first year. We added additional capacity in the cooler design to allow for upset conditions in our process and possible fouling of the coolers, and the coolers easily handle the process heat load. In cooler weather, there are long periods where the cooler fans do not even come on because the heat load is removed efficiently without need for the additional fan-induced airflow. Maintenance and operating costs on the coolers are minimal compared with a conventional evaporative cooling tower since make up water, chemical addition and blowdown costs are eliminated, which is another great feature.”
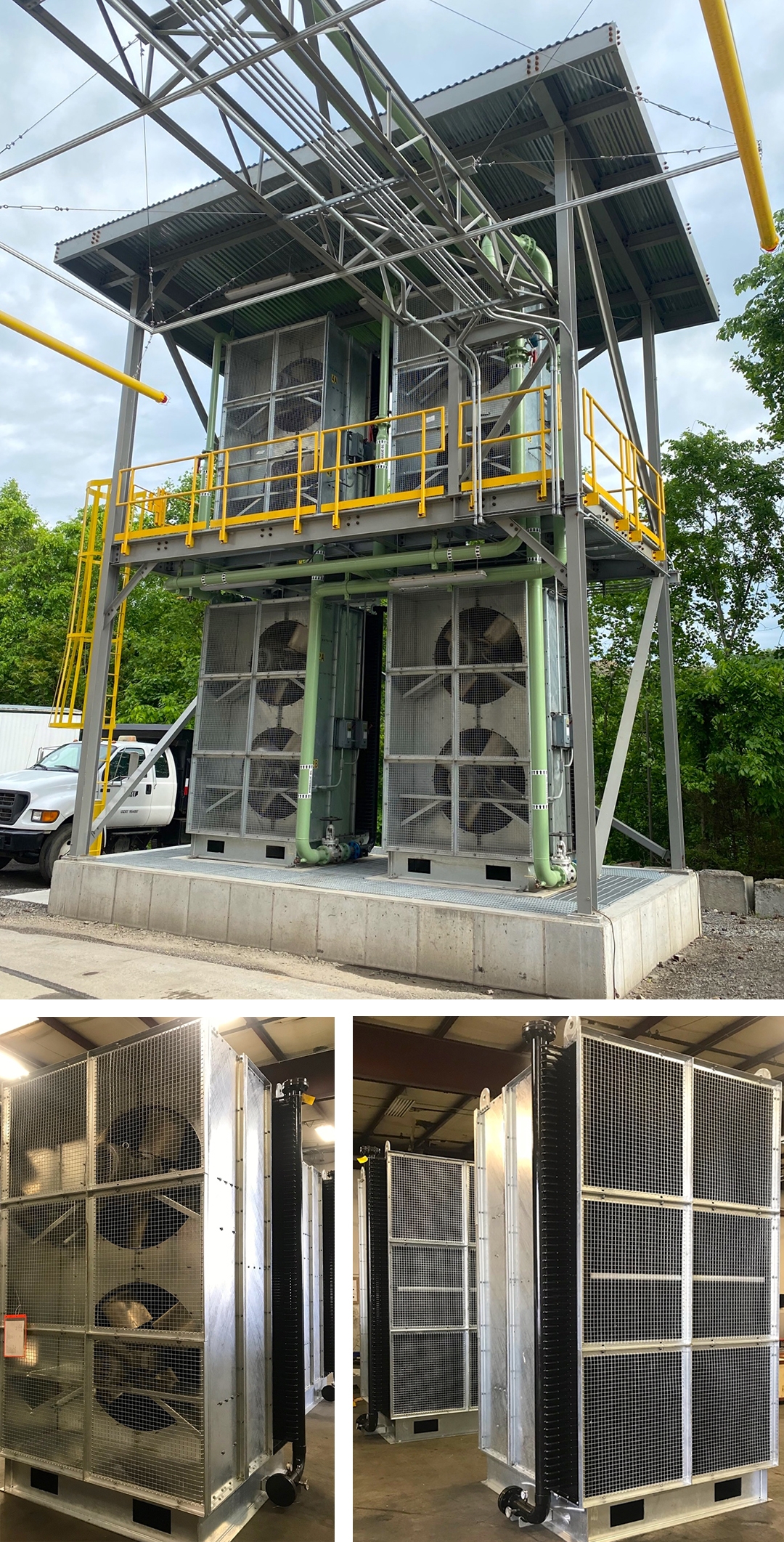
Details
- Customer: Large Industrial Forge Plant
- Location: PA
- Sector: End user
- Application: Supplemental Closed Loop Cooling System
- Product Type: Fluid-Water/Glycol Cooler